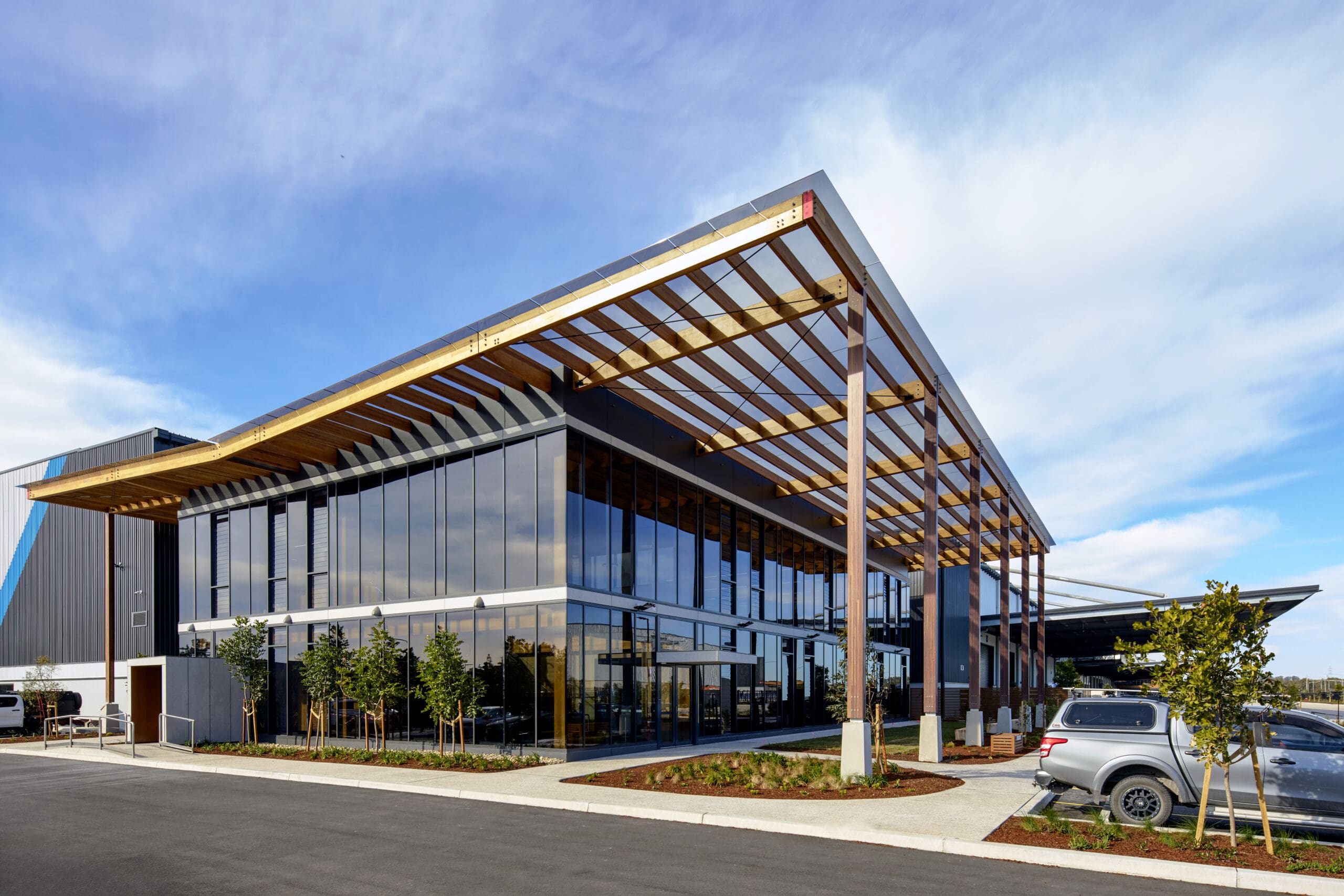
Light Horse Logistics Hub
- Civil
- Structural
- Sustainability
Over 30 Years of Partnerships in the Australian Industrial & Logistics Sector
We get it. We know what a competitive steel design looks like. We understand your critical path to getting on site, and how to plug into precinct – and intermodal-scale developments quickly and efficiently. We partner with clients to custom engineer buildings that are purpose-built to maximise the efficiency of the production, storage, and retrieval activities that happen within them.
‘Form follows Function’ is our guiding principle at the heart of industrial and logistic projects.
We’ve been applying this ethos of efficiency in partnership with our clients across the eastern seaboard of Australia for the last 30 years. Although we lean on our experience, we don’t rest on our laurels. We always look for ways to drive further efficiency in warehouses, manufacturing facilities, food & beverage temperature-controlled storage, automated fulfilment, intermodal developments, and multistorey logistics projects.
We work with developers, providing advice on how to navigate the growing number of internal and industry-led sustainability targets, advising on the engineering aspects of site selection, and delivering robust tender drawings for high-bay and multi-storey warehouses.
We also partner with builders, providing efficient steel and concrete designs and commonsense site advice that keeps things moving in the fastest-moving sector in the industry. And we work with architects, providing high quality building models for coordination, and the right amount of information early in the project to help shape up a concept.
Some of our projects include the NewCold highbay facilities in Truganina, Victoria, where we attached two 40 metre tall freezers that could fit a 10 storey apartment building inside them to an existing building; the Austral Masonry Oakdale East, New South Wales – a masonry plant, which produces many of the bricks that clad the buildings of Sydney; and Charter Hall’s Light Horse Building Hub in New South Wales, which features the first mass-timber industrial offices in Australia.
Their ability to bring an owner to the table—someone who understands the commercial drivers and can lead a responsive, efficient design process—has consistently added value. That level of engagement and accountability has played a key role in the success.
David SandersDirector, FDC Construction & Fitout
We work with D+C builders to develop cost-competitive tender designs. We have developed proprietary specialised software that allows us to optimise our designs within the tight time frames required during tenders. We love the challenge of getting our designs as light as possible.
We work with developers and project managers to take a precinct-wide approach to site servicing, levels, and sustainability.
We keep up with the fastest moving sector in the industry, able to turn around designs quickly to meet your programs.
We’re at the forefront of new construction approaches, including timber office design and offshore custom steel section sizes that use 15% less steel than conventional rolled sections.
Our multi-disciplinary team help you manage risks and constraints, including complex loading (hail, cyclonic, flood), geotechnical issues around contamination and performance, and site servicing, ahead of design development.
While you may not come across them day-to-day, and may never even step inside one, our communities depend on the goods that are produced inside industrial buildings. I’m proud of the impact our designs have on our cities.
Aaron HughesPrincipal, Structural Engineer